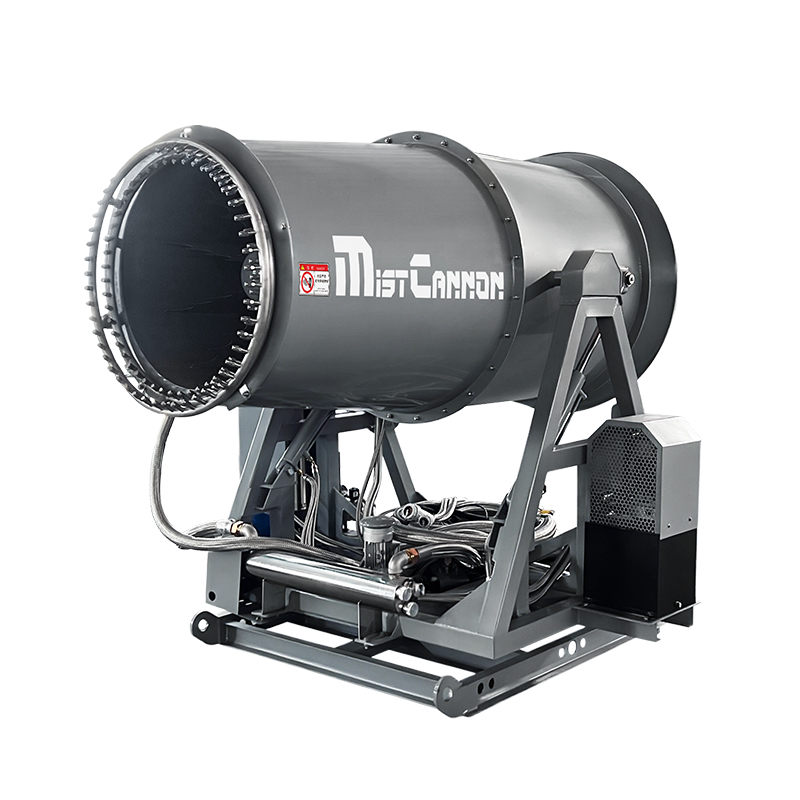
In the daily operation of coal mine bunkers, coal dust pollution looms as a constant threat—not only endangering safety (coal dust explosion critical concentration is just 30–50g/m³) but also violating strict environmental regulations (China’s Coal Industry Pollutant Emission Standard requires particulate matter ≤80mg/m³). Traditional sprinkler systems prove ineffective in enclosed/semi-enclosed bunkers, while ordinary fog cannons fail to address high-concentration coal dust and explosion-proof requirements. Specially developed for coal mine scenarios, the explosion-proof intelligent fog cannon machine is revolutionizing dust suppression with “precision particle-size capture + full-process safety control,” becoming the standard solution for bunker dust management.
Coal dust features a wide particle size distribution (0.1μm–100μm) and hydrophobic properties:
**Fine dust (<10μm)**: Forms airborne suspensions; traditional droplets >500μm struggle to adsorb
Coarse dust (10–100μm): Slow gravitational settlement; uneven atomization leads to <40% capture efficiency
Respirable dust (<5μm): Direct health hazard; traditional dust suppression machines miss over 60%
Bunkers pose electrostatic risks due to coal dust resistivity (10⁶–10¹⁰Ω·cm), making ordinary equipment dangerous:
Motor sparks risk dust explosions
Metal friction generates static electricity
High-dust environments cause frequent breakdowns
A 10-million-ton coal mine’s data:
4-hour manual inspection intervals miss real-time dust fluctuations
Post-spraying PM10 still reaches 200mg/m³ (2.5x over the limit)
Monthly shutdown losses due to dust 超标 (exceeding standards) exceed 500,000 RMB
Micron-Level Precision:
Fine coal dust (PM2.5): 20–50μm droplets (aviation-grade ceramic nozzles, particle uniformity ±2%) achieve 98% capture via Brownian motion
Coarse coal dust (PM10): 50–100μm droplets (high-pressure swirl technology) accelerate settlement 3x via inertial collision
Dynamic Concentration Linkage: Built-in laser dust sensor (accuracy ±1%) activates “intensive spray mode” when PM2.5 ≥50mg/m³, reducing concentration by 70% in 10 minutes
Intrinsic Safety Motor: Certified to Class I explosion-proof standard (Ex ib I Mb), exceeding underground coal mine requirements
Anti-Static Body: 304 stainless steel shell + conductive coating (surface resistance <10⁶Ω) eliminates static accumulation
Dust Self-Cleaning: 0.8MPa automatic filter backflushing every 15 minutes ensures long-term sensor/nozzle stability
Directed Airflow Technology: Bionic fan impeller (patent: CN2023XXXXXX) maintains 80m effective range at 10m/s wind speed ( only 50m)
Multi-Dimensional Adjustment: ±90° pitch + 360° rotation covers bunker ceilings, walls, and stockpile gaps for – free (死角 – free) dust suppression
Remote Monitoring Platform: Real-time tracking of water pressure, wind speed, and dust concentration; abnormal data pushed to control rooms in 30 seconds
Energy Optimization Algorithm: Adjusts spray frequency based on operation periods (e.g., loading/unloading peaks), saving 40% energy vs. traditional dust suppression machines
Low-Temperature Resistance: -30℃-rated water tank electric heater (5kW) ensures continuous winter operation
High-Dust Protection: IP66 rating (only IP55), fully sealed bearings extend maintenance cycles to 6 months
III. Real-World Data: A Dust Suppression Revolution in a 10-Million-Ton Bunker
Shanxi Coking Coal Bunker (500,000-ton capacity, 25,000㎡ area)
Peak dust concentration: 300mg/m³ (3.75x over the limit)
5–8 monthly shutdowns due to dust alarms
15% abnormal pneumoconiosis screenings among workers
Deployed 4 units of 100m explosion-proof fog cannon machines (2 on the ceiling, 1 on each side), integrated with the mine’s intelligent management platform
Dust Suppression Efficiency: PM2.5/PM10 stabilized at 20mg/m³/50mg/m³ (4x better than national standards)
Safety Improvement: 12 months of zero dust-related shutdowns; static accident risk reduced to 0
60% annual water savings (smart spray control)
80% reduction in manual inspection costs (95% remote monitoring coverage)
50% lower maintenance costs (self-cleaning reduces filter replacements)
Test Item | Pre-Upgrade | Post-Upgrade | National Standard |
PM2.5 Concentration (mg/m³) | 85 | 18 | ≤35 |
Explosion-Proof Rating | None | Ex ib I Mb | ≥Ex ib I Mb |
Spray Particle Uniformity | ±15% | ±2% | — |
Parameter | Ordinary Machine | Coal Mine-Specific | Selection Rationale |
Explosion-Proof | None | Class I Certification | Mitigate bunker explosion risks |
Particle Control | Single Size | 20–100μm Adjustable | Adapt to multi-size coal dust |
Sensor Accuracy | ±5% | ±1% | Real-time concentration linkage |
Protection Rating | IP55 | IP66 | Long-term high-dust operation |
Fully Enclosed Bunkers: Prioritize ceiling-mounted fog cannons (space-saving), with air deflectors to direct mist downward for deep stockpile suppression
Semi-Open Yards: Add wind-speed compensation (response time <2s); increase spray pressure automatically at >8m/s to maintain range
Transfer Points: Deploy small fixed dust suppression machines (30m range) linked to conveyor belts for instant dust suppression during material transfer
Pseudo-Explosion-Proof Traps: Some manufacturers only (explosion-proof) motors, ignoring sensors/wiring; verify full machine type-test reports
False Parameter Claims: Demand on-site bunker test data (not lab data), especially dust suppression efficiency at 10m/s wind speed
Under the Coal Mine Safety Production Standardization System (2023 Edition), dust suppression machine purchases qualify for:
10% corporate income tax credit on safety equipment investments
Up to 25% special subsidies for environmental protection equipment
Smart transformation loans with 30% lower interest rates
A coal mine example: 8 explosion-proof fog cannon machines (total 2.4M RMB) qualify for 600K RMB subsidies, reducing effective cost to 1.56M RMB with payback in 14 months.
Upgrading dust suppression in coal mine bunkers is a strategic balance of safety investment and economic efficiency. When explosion-proof fog cannon machines achieve “98% coal dust capture + accident-free operation,” they become more than just environmental equipment—they’re safety firewalls and catalysts for intelligent transformation. Under dual policies of “carbon neutrality” and safety production, choosing solutions truly adapted to coal mine scenarios ensures compliance, worker health, and operational efficiency.
Contact With Us
If you have any questions please fell free to contact with us.